Remote Monitoring Comes to Kansas State’s Feed Mill
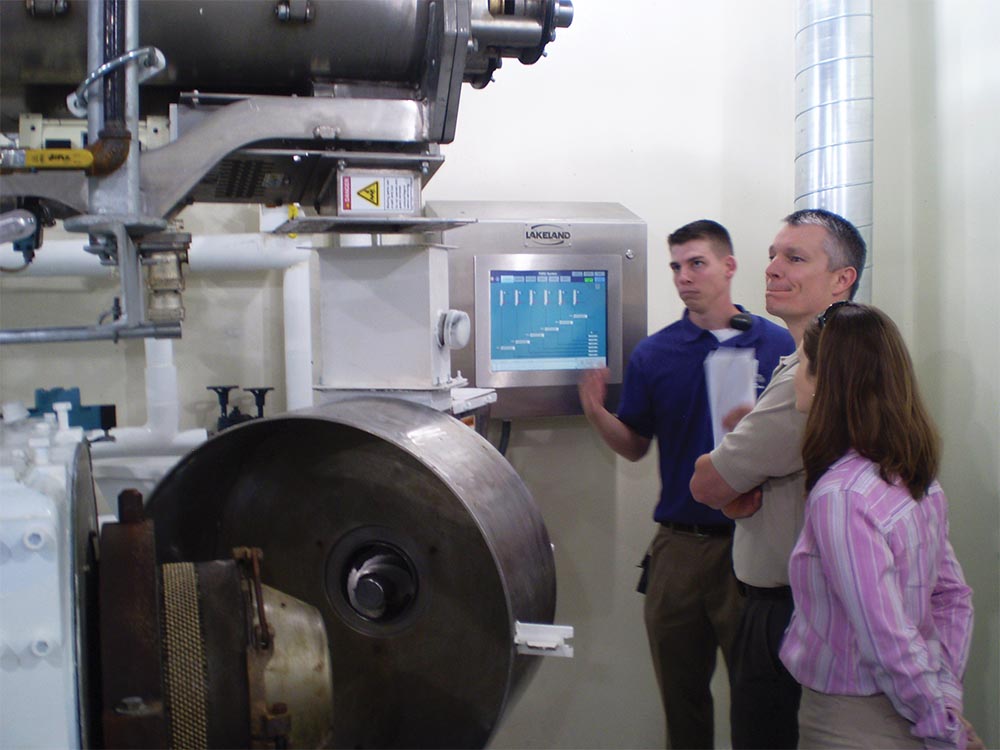
By: Grant Gerke
Published: September 21, 2015
In 2014, Kansas State University (KSU) unveiled the sprawling $16 million O.H. Kruse Feed Technology Center in Manhattan, Kan., that houses a 5 tons/hour production feed mill and a Feed Safety Research Center (FSRC). The 142-foot-tall building rises over the campus much in the same way the Kansas State Feed Science and Management program does in the animal feed industry. This well-known program has had close to 700 graduates find employment in the U.S. food manufacturing industry over the past 60 years.
With rapid changes in the food industry, most notably with the Food Safety Modernization Act (FSMA), there’s been an emphasis on grain safety within the industry and the need to educate the workforce. The FSRC educates students in food safety process applications and is the only hazard level II feed research center in the world.
The FSRC’s mission statement includes identifying, improving and experimenting with animal feed in the batch process. The center produces feed pellets, using a conditioning machine that infuses steam into ground-up corn and then presses it into pellets. The steam conditioning is the thermomechanical process variable; changing the amount of pressure can increase pellet quality.
The experimentation often involves adding pathogens to the feed production process, such as salmonella, and then remotely controlling and monitoring the application. The research center uses Tatsoft’s FactoryStudio to allow students and faculty to remotely monitor whether process variable changes can eliminate bacteria.
“The research center has a PC-based SCADA HMI station that’s in the mill for normal process operations, but they also display those same (HMI) screens on iPads or smartphone devices,” says Mark Spindler, CTO at the Lakeland Companies.
Lakeland integrated the controls and automation at the FSRC and leveraged FactoryStudio’s native ControlLogix communication drivers for the remote monitoring architecture. Using ControlLogix-defined tags and data structure saved Lakeland time with the integration because they eliminated the need for manual configuration of tags that is typically required when building a SCADA system.
“So once we configured the PC/HMI in the operations area with different security profiles, we were ready to make it available for remote monitoring via an intranet network and then to iPads,” Spindler says.
The SCADA system offers a wide range of process setup tags, such as type and how-to measurements in digital, analog or date/time format. Setup tags include start value, an option to retain a value when you power down the system, and multidimensional tags. Those can be applied to motors, pumps or machinery.
Remote monitoring is especially important for the safety center, where pathogens can be observed and controlled from the classroom. According to Kansas State, students and faculty monitor the process experiments on clear, plastic-covered iPads inside the safety research center. With an EtherNet/IP communication backbone, students connect to iPads and iPhones with the Tatsoft app.
The experiments are paying off, too. A pig virus known as porcine epidemic diarrhea virus (PEDv) infects older hogs and young piglets. For the piglets, it means death, while older hogs lose weight. “Through the activity at FSRC, Kansas State has been able to develop a procedure to help stop the spread of PEDv,” says Cassandra Jones, assistant professor of feed technology at Kansas State.
Food ingredient management
While the real-world SCADA system provides remote monitoring in Kansas State’s safety research center, a food ingredient management system is providing a glimpse of high-level food traceability to the future workforce. Besides the research center, the Kruse Feed Center includes a production feed mill that supplies the university’s animal science department on a daily basis.
Interstates Control Systems, a control systems integrator, provided I-Control and HMI integration services for the feed mill production facility. I-Control is a food ingredient database management system that gathers data from a batch process, create reports and can export data into an enterprise resource planning (ERP) system. It includes all system data, from PLCs that communicate with equipment to storing food recipes. The food ingredient software is primarily designed for the feed, pet food, pre-mix and flour milling industries.
The I-Control platform provides an introduction to modern food traceability, beginning with automated routing controls for when ingredients enter the receiving area. For batch processing, the food ingredient management system measures dry and liquid ingredients. The food system includes enforced strict sequencing rules and a “hand-add” function that is also regulated and tracked.
According to Interstates, during the pellet and extruding process, the management system constantly monitors the pellet mill for quality and production output, while the load-out module manages production from the storage bins to the actual customer